Был у меня ЧПУятор, который я благополучно разобрал (в планах пересборка пока не значится). Но Ватсон без трубки уже не может, так что мне захотелось, всё же, иметь что-то эдакое, ЧПУяторное. И взалкал я трипечатор (3Д принтер), и приобрёл дешёвый китайский комплект для сборки. Теперь вечерами собираю; потихоньку, по часу-двум в день, поэтому так долго.
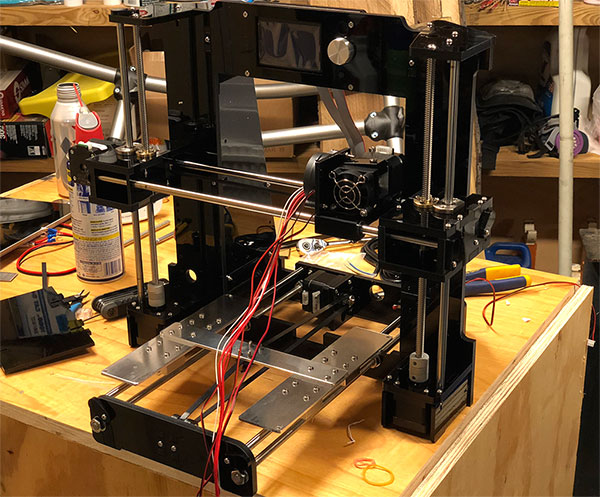
Это трипечатор Anet A6, который по сути является форкнутой копией Reprap Prusa. Только в Прусе мозги Arduino+Ramps+DRV8825, а тут одна разработанная с нуля плата “три-в-одном”, хотя по сути на ней то же самое — ATmega 1284P и те же самые драйверы шаговиков от Техасских Инструментов. Не знаю, можно ли залить туда другую прошивку (например, Marlin или Teacup); и не факт, что это что-то даст, кроме ухода от проприетарности.
Вообще, трипечатор, если разобраться, представляет собой 4-осный ЧПУятор: 3 координатных оси плюс ось экструдера. Его мозги переваривают стандартнейший G-code; поэтому у меня есть ещё пара задумок по поводу, например, замены экструдера на лазер, и вырезания и гравирования всякого. Правда, лазер нужной мощности (надо, как я понимаю, не менее пяти ватт), скорее всего, будет стоить больше, чем этот принтер, даже если покупать его в Алиэкспрессах. Кроме того, тут есть серьёзные ограничения по рабочему полю — 8×8 дюймов (200x200mm) это всё, что оно может. Но это так, дальний прицел. Для начала хорошо бы разобраться с тем, для чего оно, собственно, предназначено.
Зачем оно мне? Ну, наиболее мне интересное — это изготовление разного рода корпусов под мои электронные проекты. А то усилитель для наушников я фактически доделал, а сунуть его некуда. Не в рассыпухе же им пользоваться.